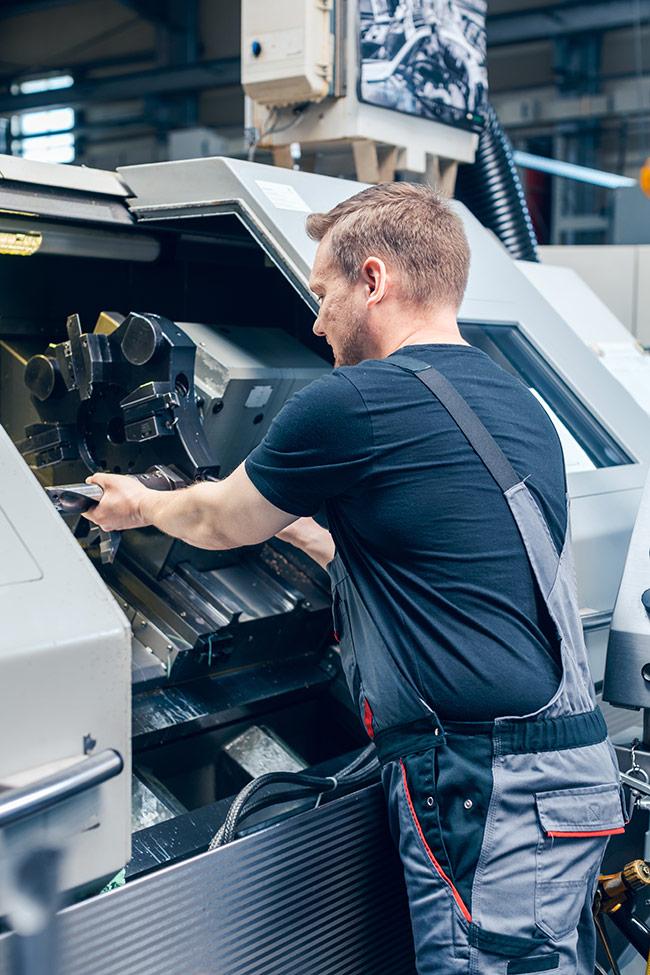
Precision, Performance, Reliability: Top-Tier CNC Repair Service
Welcome to our blog page, where CNC machine enthusiasts come together to explore the secrets of seamless maintenance. Join our community of CNC caretakers as we dive into the world of machine TLC. You know how to CNC—now, learn how to care for your machines! From clever hacks to preventative maintenance strategies for your machinist tools, we’ve got you covered!
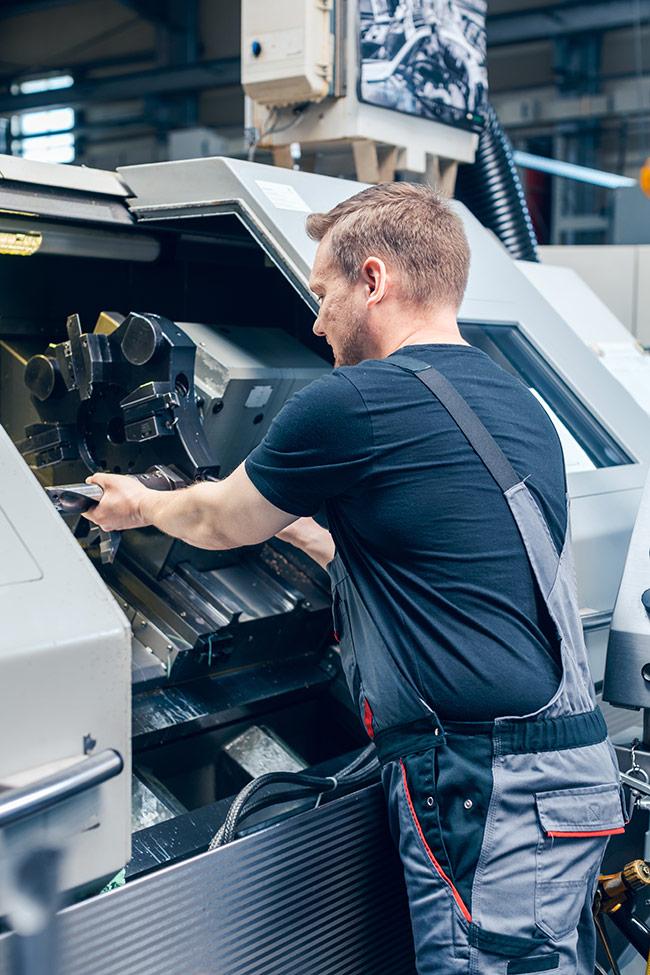
Precision, Performance, Reliability: Top-Tier CNC Repair Service
First thing to remember, At In-House CNC Service, we are your trusted partner for comprehensive CNC repair service solutions. For example, with our unrivaled expertise, extensive experience, and unwavering commitment to excellence, we guarantee that your CNC machines receive the utmost care and attention they deserve.
We ensure your shop runs at peak productivity.
We ensure your shop runs at peak productivity.
Our mission is to optimize machine performance, enhance productivity, and ensure operations run at peak efficiency. When it comes to CNC repair service, rely on us for unmatched quality and superior results.
Tailored Solutions for Your Unique Needs
Precision, reliability, and productivity are the driving forces behind operational success. Bearings, as vital components of CNC machines, are fundamental to smooth operation, minimizing friction, and preserving the high levels of accuracy required for optimal performance.
Our technicians are highly experienced and possess comprehensive knowledge of CNC machine components. Whether it’s a spindle, motor, or any other critical component, we have an in-depth understanding of each part’s function and its essential role in maintaining machine performance.
We offer comprehensive third-party pre-purchase inspections that provide a detailed assessment of a machine’s condition and performance. Our experts personally review the findings with you, addressing any concerns and ensuring complete clarity and confidence in your investment.
It is essential to keep your CNC machines updated with the latest software upgrades and optimization techniques to maximize performance and efficiency. For this reason, our technicians continuously stay informed on the latest software releases and upgrades from CNC machine manufacturers, ensuring your equipment remains at peak capability.
Keeping your CNC machines up to date with the latest software upgrades and optimization techniques is crucial for maximizing their performance and efficiency. That’s why our technicians stay current with the latest software releases and updates from CNC machine manufacturers, ensuring your equipment operates at peak performance.
We provide professional machine dismantling, installation, and shipping preparation services to ensure a seamless transition for your CNC machinery. Whether you are relocating equipment, preparing for shipment, or installing new machines, our specialized expertise guarantees a smooth and efficient process.
CNC Preventative Maintenance
Service Offerings and Expertise
CNC Maintenance: Precision Pays, Downtime Doesn’t
Don’t let your CNC machine turn into a high-tech paperweight! Instead, sign up for our maintenance service like you are booking a health spa for your machinery! By all means, it’s pampering, caring, and comes out performing at its best. So why risk unexpected downtime and possible headaches? Be proactive, let’s give your CNC the “service spa” treatment it deserves. Remember, a well-maintained machine is a happy, high-producing machine.