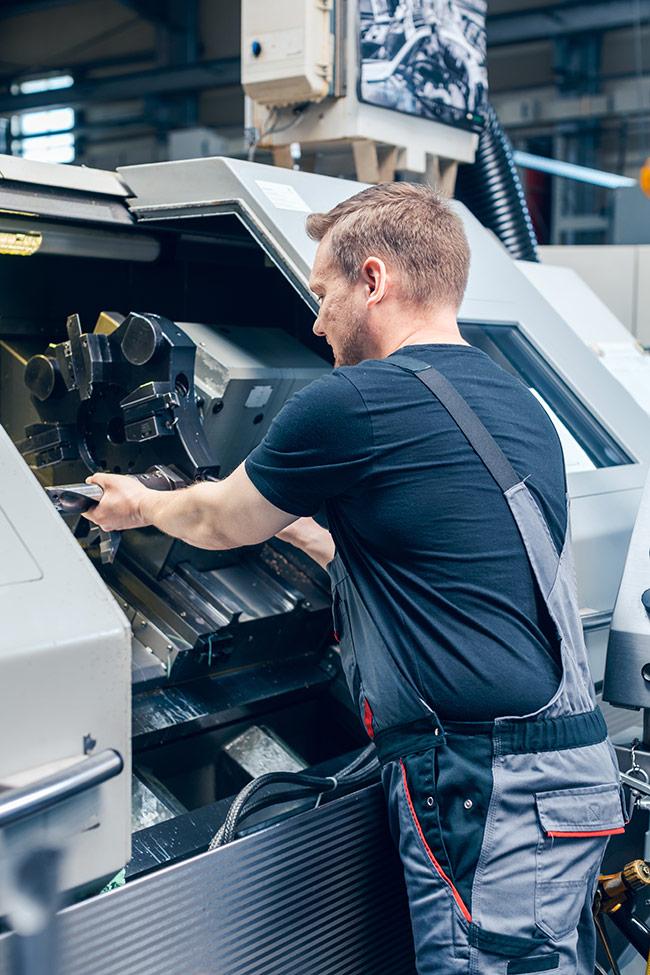
In-House CNC Service:
CNC Preventative Maintenance
Why Choose Our CNC Preventative Maintenance Service?
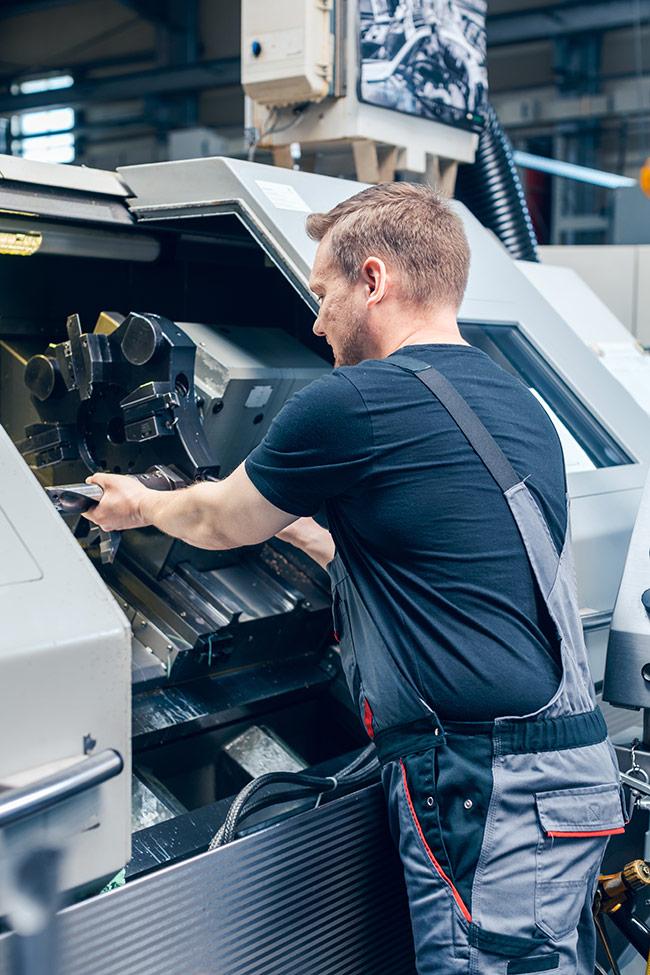
In-House CNC Service:
CNC Preventative Maintenance
Why Choose Our CNC Preventative Maintenance Service?
Maximize CNC Machine Performance with Preventative Maintenance
CNC machines require regular maintenance to ensure peak performance, accuracy, and longevity. Without a proactive maintenance plan, wear and tear can lead to unexpected breakdowns, costly repairs, and production delays.
At In-House CNC, we provide expert preventative maintenance services designed to reduce downtime, extend machine life, and optimize operational efficiency. By identifying potential issues before they escalate, we help you keep your equipment running smoothly and reliably.
Key Features of Our CNC Preventative Maintenance Services
Routine Inspections to Prevent Breakdowns
Regular performance checks and diagnostic inspections help identify wear, misalignment, and early signs of failure before they cause costly downtime. Our experts ensure your CNC machines remain in optimal working condition.
Comprehensive System Maintenance
We service critical machine components, including cooling systems, lubrication systems, spindles, and electrical connections. Our maintenance approach helps reduce friction, prevent overheating, and maintain precision in every production run.
Customized Maintenance Plans for Your Equipment
Every CNC machine has unique needs. We develop tailored maintenance schedules based on machine usage, operating conditions, and manufacturer recommendations, ensuring maximum efficiency and longevity.
At In-House CNC, our preventative maintenance solutions help you avoid unexpected breakdowns, reduce repair costs, and keep production running smoothly.
Creating a CNC Preventative Maintenance Schedule
Daily Maintenance Tasks – Routine daily checks help catch small issues before they escalate. This includes monitoring coolant levels, inspecting lubrication systems, and cleaning key components like tool holders and chip conveyors to prevent buildup.
Weekly Maintenance Tasks – A more in-depth inspection should be performed weekly, including checking electrical connections, inspecting belts for wear, and ensuring the cooling system is functioning properly. These proactive steps help maintain consistent machine performance.
Monthly Maintenance Tasks – Monthly maintenance involves detailed inspections of all major machine components, including spindle alignment, backlash checks, and lubrication system flushing. Identifying minor misalignments early prevents costly repairs later.
Quarterly Maintenance Tasks – Every few months, a comprehensive system evaluation should be performed, including deep cleaning, full system calibration, and wear analysis. This ensures your CNC machine continues to operate at peak efficiency and precision.
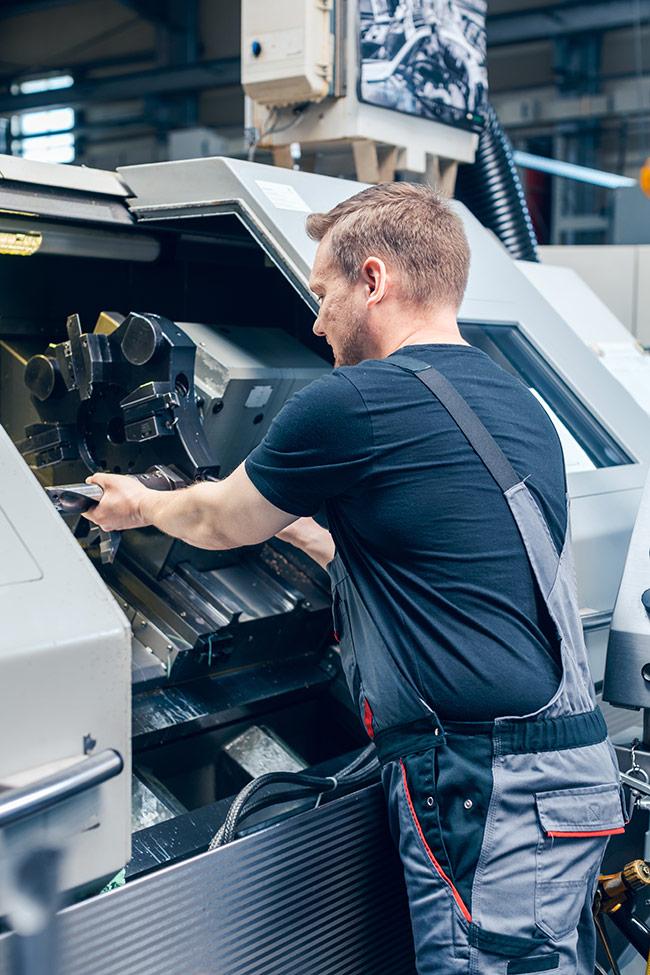
Key Maintenance Tasks for CNC Machines
Monitor and Maintain Coolant Levels
Proper coolant levels are essential for temperature regulation and preventing overheating. Regularly checking and cleaning the coolant tank ensures smooth operation and extends tool life.
Inspect and Lubricate Moving Components
The lubrication system reduces friction and wear on moving parts. Regular checks ensure consistent lubrication flow, preventing premature bearing and spindle wear.
Check Electrical Connections for Wear
Loose or damaged electrical components can cause intermittent failures and unexpected downtime. Regular inspections help catch wiring issues, power fluctuations, and failing connections before they cause disruptions.
Monitor Backlash for Precision Control
Backlash in the CNC system can lead to positioning errors and decreased accuracy. Periodic checks ensure that machine components remain tight, aligned, and functioning at peak precision.
Common CNC Preventative Maintenance Issues
Coolant Contamination and Buildup
Coolant can become contaminated with debris, oil, or bacteria, leading to poor machine performance and potential damage. Regular filtering and tank cleaning prevent contamination and ensure optimal cooling efficiency.
Inadequate Lubrication Leading to Excessive Wear
If the lubrication system is not maintained, moving parts can become dry and wear out prematurely. Regularly checking lubricant levels, flow rates, and delivery lines helps prevent friction-related failures.
Overheating Due to Poor Cooling System Maintenance
Dust, debris, or low coolant levels can cause CNC machines to overheat, leading to component damage and system failure. Routine cooling system cleaning and inspections ensure consistent thermal control.
Electrical Failures from Worn Components
Loose or failing electrical connections can lead to power surges, erratic performance, or sudden shutdowns. Regular wiring inspections and component testing help catch electrical issues before they cause downtime.
By addressing these common maintenance issues proactively, you can enhance reliability, prevent unexpected failures, and keep your CNC machines running at peak performance.
Partner with In-House CNC for Preventative Maintenance Services
At In-House CNC, we provide comprehensive preventative maintenance services to keep your CNC machines operating at peak performance and efficiency. Our expert technicians follow structured maintenance schedules, conduct thorough inspections, and perform essential servicing to prevent unexpected failures.
Whether you need routine system checks, lubrication management, cooling system maintenance, or electrical inspections, we tailor our services to meet the specific needs of your equipment. Contact us today to schedule your CNC preventative maintenance service and ensure your machines stay in top working condition.
Prevent Breakdowns with Expert CNC Preventative Maintenance
Unplanned downtime and costly repairs can disrupt production schedules and impact efficiency. A structured preventative maintenance program ensures optimal machine performance, extended lifespan, and consistent precision.
At In-House CNC, our expert maintenance services help you detect issues early, reduce wear, and prevent costly breakdowns. Keep your CNC machines running at peak efficiency—schedule your preventative maintenance service today.