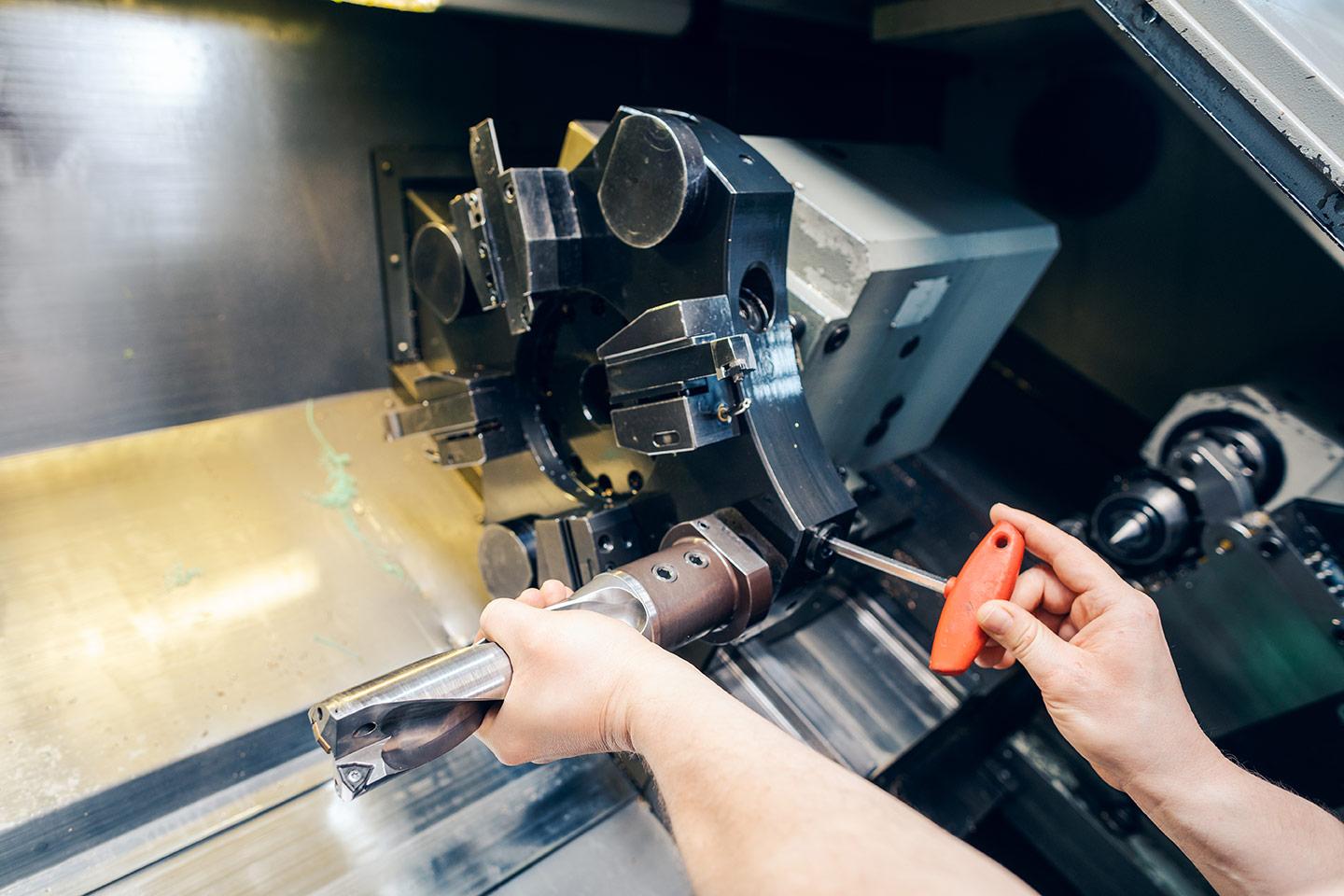
In-House CNC Service:
Routine Inspection
Why Choose Our Routine Inspection Service?
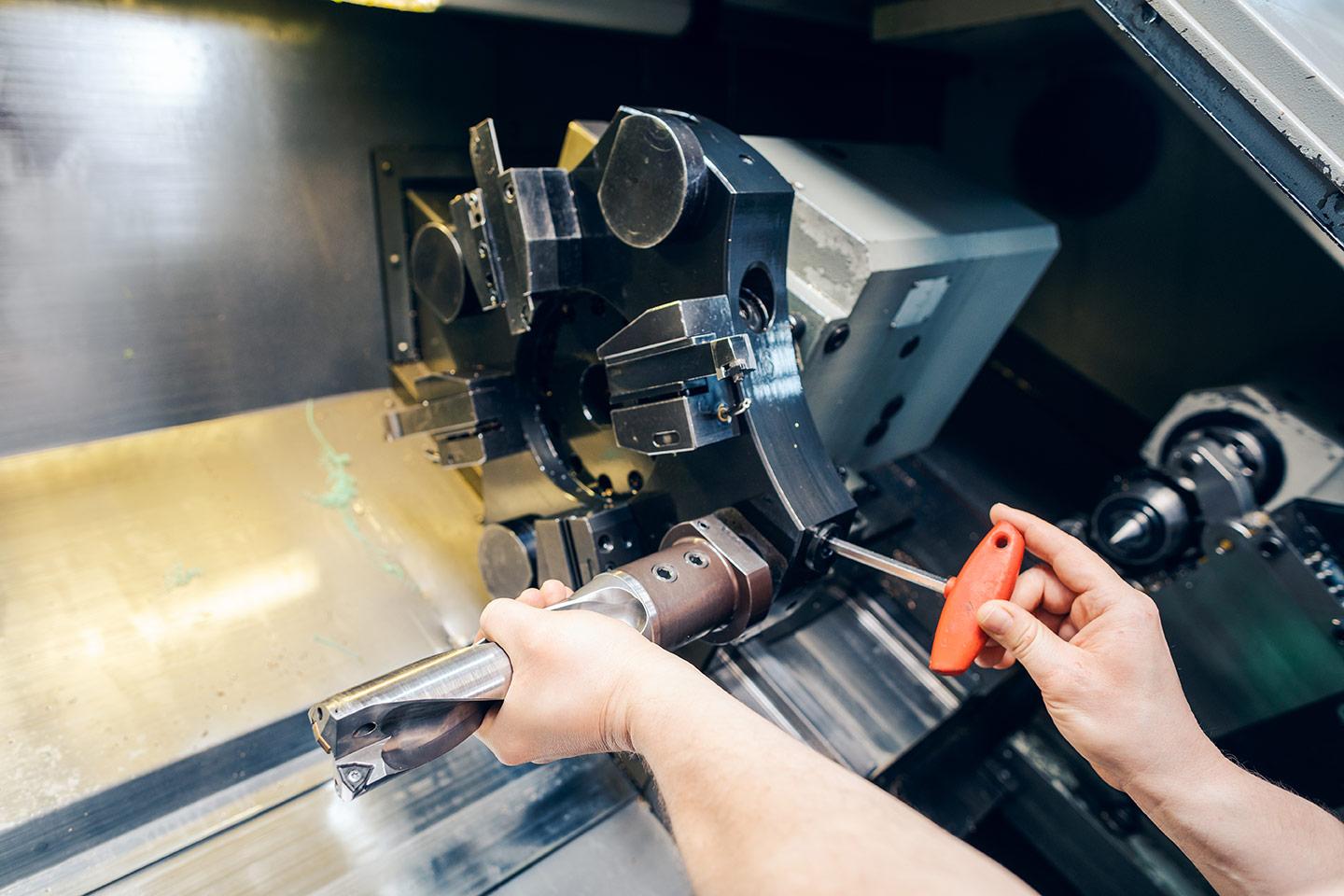
In-House CNC Service:
Routine Inspection
Why Choose Our Routine Inspection Service?
Optimize CNC Performance with Routine Inspections
Routine inspections are essential for maintaining the precision, efficiency, and longevity of your CNC machines. By proactively assessing machine health, you can detect minor issues before they escalate into costly repairs or unexpected breakdowns. Regular inspections not only extend equipment lifespan but also help ensure workplace safety and consistent machining accuracy.
At In-House CNC, we provide expert CNC inspection services to help you prevent downtime, optimize performance, and keep your operations running smoothly. Our comprehensive approach covers all key components, ensuring your machines deliver precise, reliable results every time.
Key Benefits of Routine CNC Inspections
Prevent Costly Repairs and Extend Machine Life
Regular inspections help identify minor issues such as misalignments, worn components, or calibration drift before they lead to expensive repairs. By addressing these early, you can extend the lifespan of your CNC machine and avoid unexpected failures that disrupt operations. Preventative maintenance not only saves money on repairs but also ensures long-term reliability and efficiency.
Minimize Downtime and Production Delays
Unplanned downtime can halt production, leading to missed deadlines and lost revenue. Routine inspections help detect mechanical wear, lubrication issues, and system inefficiencies before they escalate into major problems. Keeping machines in top condition reduces operational disruptions and keeps your production running smoothly.
Ensure Machining Accuracy and Consistency
Even minor calibration issues can affect precision, leading to inconsistent parts, material waste, and rework. Routine inspections verify tool alignment, axis positioning, and spindle accuracy to maintain tight tolerances. By ensuring consistent machining quality, you can meet production standards while reducing scrap and errors.
Enhance Workplace Safety
Worn-out components, faulty wiring, or uncalibrated equipment can create safety risks for operators. Routine inspections ensure all safety features, emergency stops, and mechanical safeguards function correctly. Preventing equipment malfunctions helps maintain a safe and productive work environment.
CNC Inspection Schedules: Daily, Monthly, and Annual Checks
Routine inspections keep CNC machines running efficiently and help prevent costly breakdowns. Daily inspections involve quick checks for lubrication levels, tool wear, and misalignment to catch minor issues early. Monthly inspections focus on belts, filters, and cooling systems to maintain smooth operation.
Quarterly inspections dive deeper into drive systems, alignment accuracy, and electrical components to prevent performance issues. Annual inspections provide a full-system evaluation, ensuring long-term reliability and precision. Following a structured inspection schedule extends machine life, improves efficiency, and reduces downtime.
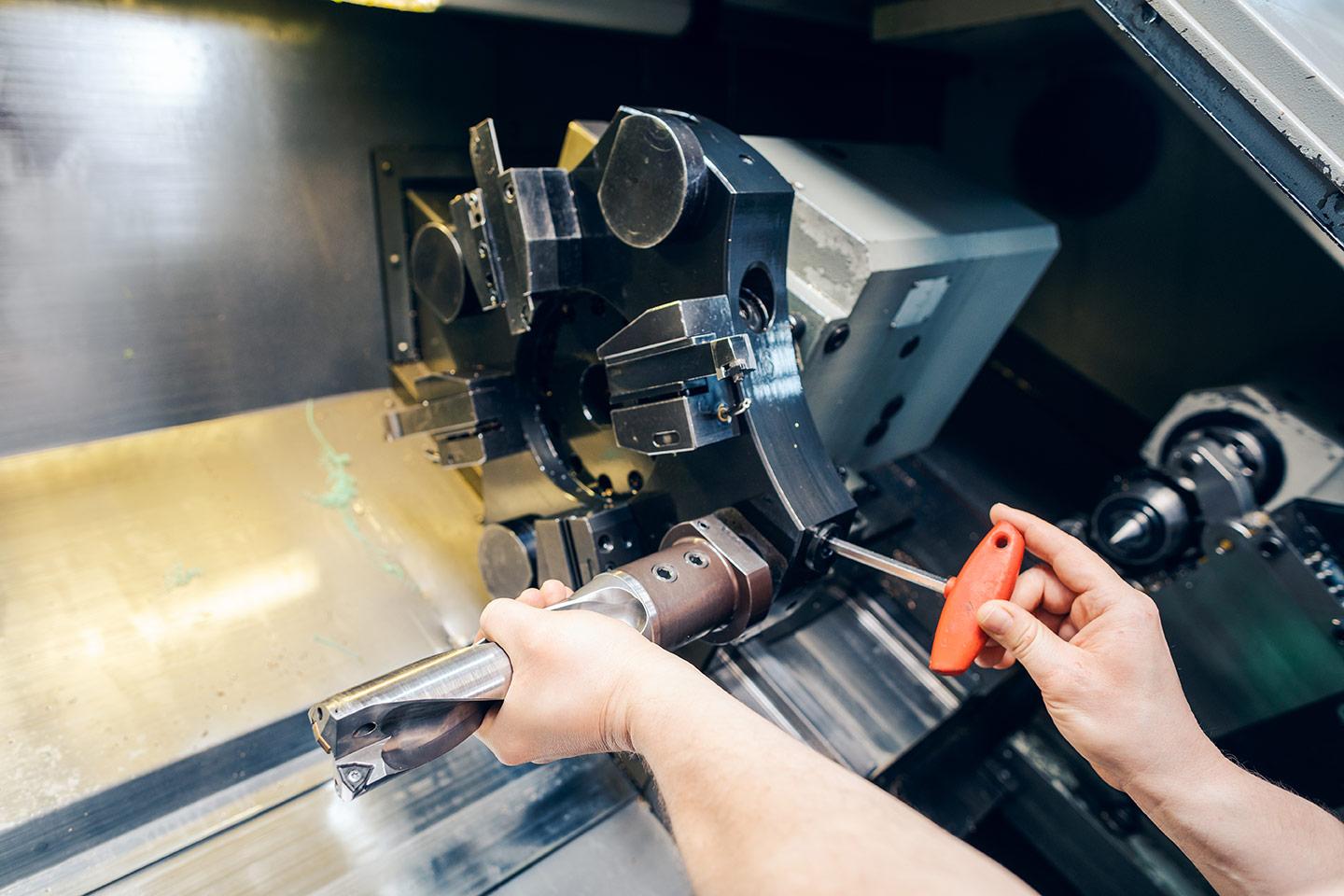
What’s Included in a CNC Machine Inspection?
Mechanical Component Assessment
Regular wear and tear on mechanical components can lead to misalignment, vibration issues, or premature failure. We inspect belts, gears, bearings, and tool holders for signs of deterioration, ensuring all parts function smoothly. Addressing mechanical wear early helps maintain machining accuracy and prevents costly breakdowns.
Lubrication System Check
Proper lubrication reduces friction and prevents excessive heat buildup, which can lead to component wear or even system failure. We verify that all moving parts receive adequate lubrication, replacing fluids or grease as needed. Keeping the lubrication system in top condition extends the life of critical components and optimizes performance.
Electrical System Evaluation
Preventative maintenance services make sure machines keep running smoothly. By regularly lubricating moving parts, testing cooling systems, and checking electrical systems, you prevent small issues from growing into major machine repair needs.
Precision Calibration and Alignment
Over time, CNC machines can lose accuracy due to gradual shifts in alignment and calibration. We assess spindle alignment, axis positioning, and geometric accuracy to ensure precision machining. Routine calibration checks help maintain tight tolerances, improve part quality, and minimize rework.
CNC Machine Repair and Preventative Maintenance
When inspections uncover issues, timely repairs are essential to prevent further damage and costly downtime. Our CNC repair process begins with a thorough inspection to diagnose mechanical, electrical, or software-related problems. Once identified, we repair or replace faulty components, ensuring your machine is restored to optimal condition. After repairs, we recalibrate and test the system to verify accuracy, alignment, and smooth operation.
Preventative maintenance, including lubrication, cooling system checks, and electrical testing, keeps your CNC machine running efficiently and reduces the risk of unexpected failures. Regular maintenance helps extend equipment lifespan, improve performance, and minimize costly disruptions.
Ensure Peak CNC Performance with Routine Inspections
CNC machine downtime, precision errors, and mechanical failures can impact your bottom line. Routine inspections prevent costly disruptions by ensuring your equipment remains in optimal condition.
At In-House CNC, we specialize in preventative maintenance and machine inspections to keep your operations running smoothly. Our expert technicians provide detailed assessments and proactive solutions to maximize uptime and efficiency.
Don’t wait for a breakdown—schedule your CNC inspection today and keep your machines operating at peak performance.